Hydrieranlage
- Verfügbarkeit Auf Bestellung
- Hersteller Armfield
- Artikelnr. FT67
- Produkt angesehen: 24792
Teilen:
Hydrieranlage
MINIATURE-SCALE R&D TECHNOLOGY
FT67 Hydrieranlage
Die Armfield Hydrieranlage ist ein Stand-Chargen-Bearbeitungsbehälter, der verwendet wird, um den Sättigungsgrad von Speiseölen in 25-Liter-Chargen einzustellen.
Features
• Stainless steel pressure vessel
• Vacuum liquid ring pump
• Extraction pump
• Pressure leaf filters
• Air driven agitators
• Integral steam heating coil and cooling coil
• Temperatures to 180°C
• Safe zoned controls
• Accurate control of hydrogen addition
Benefits
> Only 25 litres of oil to be hydrogenated
> Safe and easy to use
> Reusable filter mesh
Description
The main processing vessel is situated in a floor standing stainless steel framework which also houses a catalyst mixing tank, filter pump, pressure leaf filter and vacuum pump. All equipment in contact with the process fluid is manufactured from stainless steel.
The hydrogenation vessel has a batch capacity of 25 litres. It is a vertical cylindrical vessel which incorporates a cooling/steam heating coil, hydrogen gas sparge ring, variable speed turbine agitator and baffle arrangement.
The hydrogen addition cycle results in an exothermic reaction and maintenance of the operating temperature is achieved by circulating metered cooling water through the submerged cooling coil which removes the excess heat from the reaction.
Initial heating to the reaction temperature is by steam, also in the immersed coil. A steam pressure control station allows pressures of up to 10.0 bar on the coil so that process temperatures of up to 180°C can be achieved.
Adjusting the rotational speed of the turbine agitator air motor
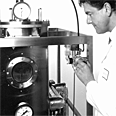
The turbine agitator is driven by a pneumatic motor through a mechanical seal in the lid of the vessel. Rotational speed is varied by adjusting the pressure of the compressed air driving the motor. A maximum speed of 2500 rpm* can be achieved.
The propeller mixer in the catalyst preparation tank is also driven by pneumatic motor and is capable of rotating at speeds up to 850 rpm*.
Pneumatics are used as the motive force as the presence of hydrogen gas requires the use of the minimum of electrical com-ponents. Only the filter charge pump and the liquid ring vacuum pump are driven by electric motor.
The centrifugal filter charge pump allows efficient filtering of the catalyst from the oil by the pressure leaf filter which is a reusable filter requiring no replacement of the filter element. If necessary, filter aid in the form of a diatomaceous earth can be mixed in the catalyst tank and added to the oil charge prior to filtering.
The process vessel and filter are designed fully in accordance with the BS 5500 code for pressure vessels. Vacuum levels of 65 mbar are achieved in the reactor vessel by the liquid ring vacuum pump. Reduced system pressures are necessary to prevent oxida-tion during the heating cycle and assist in the removal of any water present in the oil. Also, the suction pressure is used to charge the vessel with oil and for the addition of catalyst and filter aid.
* - no load condition.
Modes of Operation
In order to increase the degree of saturation of edible oils to adjust their physical characteristics, the oil must be mixed with hydrogen gas in the presence of a catalyst under very precisely controlled process conditions. On completion of the reaction, the catalyst must be completely removed by an efficient filtration operation.
The Hydrogenation unit achieves this by use of a variable speed turbine impeller and baffle arrangement which allows efficient gas-liquid mixing, and accurate control of the pertinent process parameters.
Oil is heated to the desired reaction temperature then hydrogen gas is admitted and fills the vapour space to the pressure required. The progress of the reaction is monitored by regular sample taking and the process stopped when the desired degree of saturation has been obtained.
The Filtration Process
A pressure leaf type filter is used to filter out the catalyst. Due to the small quantities of catalyst involved, diatomaceous earth is often added to the oil as a filter-aid. This type of filter is the standard used in industry for this duty and provides a convenient method for familiarisation with the operating sequence of such a filter.
Performance
As a guideline to the performance of the hydrogenation unit, typically, using 0.05 - 0.1% active nickel and pure hydrogen, the iodine value (degree of saturation) of cottonseed oil will reduce from 108 to 70 in 40-60 minutes.
Test results from the University of Leeds - Dept. of Food Science
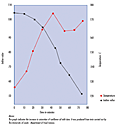
Samples showing increasing hardness of the oil with process time
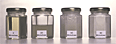
Unit Specifications
All electrical equipment used on the unit is scheduled flameproof suitable for use in a zone 1 area, which is an area in which an explosive gas-air mixture is likely to occur in normal operation. Due to the use of hydrogen gas, the hydrogenation unit must be installed in an area designated as safe.
Relevant local regulations regarding the operation of this type of equipment must be adhered to.
Hydrogenation Vessel:
Total volume: 46.0 litres
Working volume: 25.0 litres
Cooling/heating coil surface area: 0.08m2
Maximum working temperature: 180°C
Normal working pressure: 0.7bar and 65 mbar.
Max working pressure: 2bar
Agitator drive: Pneumatic motor/gearbox
Maximum speed: 2500 rpm
Catalyst Tank:
Volume: 4.0 litres
Stirrer: Pneumatic drive, to 850 rpm
Filter Pump:
Type: Centrifugal
Impeller: Closed
Capacity: 100 l/m @ 2.75 bar
Liquid Ring Vacuum Pump:
Capacity: 66.0m3/hr
Sealant: Water
Sealant flow rate: 6.0 l/m
Normal operating pressure: 65 mbar
Pressure Leaf Filter:
Material: Stainless steel
Filter volume: 3.8 litres
Filter cake capacity:1.0 litre
Filtering area: 0.09m2
Filter screen: 110 mesh (0.3mm wire)
Maximum pressure: 3.0 bar
Requirements
Electricity
FT67-C: 415V/3ph/50Hz, (6.5kW)
FT67-D: 208V/3ph/60Hz, (8.5kW)
FT67-E: 380V/3ph/50Hz, (6.5kW)
FT67-F: 220V/3ph/60Hz, (8.5kW)
Cooling Water
20.0 l/m @ 3.0 bar min - 5.0 bar max pressure
Steam Supply
100.0 kg/hr @ 10.0 bar min. pressure
Compressed Air
25.0 l/s @ 6.0 bar min - 10.0 bar max pressure
Shipping Specification
Overall volume: 2.5m³
Gross weight: 500kg
Overall Dimensions
Height: 1.85m
Width: 1.25m
Depth: 0.95m